KX-2 – Collaborative Laboratory Robot
For flexible, safe and reliable laboratory automation, look no further than the innovative kx-2 collaborative laboratory robot.
The KX-2 collaborative robot has three vertical travel options, 500mm,
750mm and 1000mm, providing process optimisation and increased
throughput for your laboratory.


Explore the future of laboratory automation with the KX-2
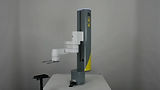
Discover the pinnacle of laboratory automation with the KX-2, where innovation meets collaboration. Offering unparalleled flexibility, safety, and reliability, the KX-2 is engineered to optimize processes and enhance throughput in your laboratory operations.
Equipped with three vertical travel options – 500mm, 750mm, and 1000mm – the KX-2 ensures seamless adaptation to your workflow requirements. Its full enclosure design guarantees intrinsic safety, while proven PRI technology delivers consistent and reliable performance, meeting all your automation needs.
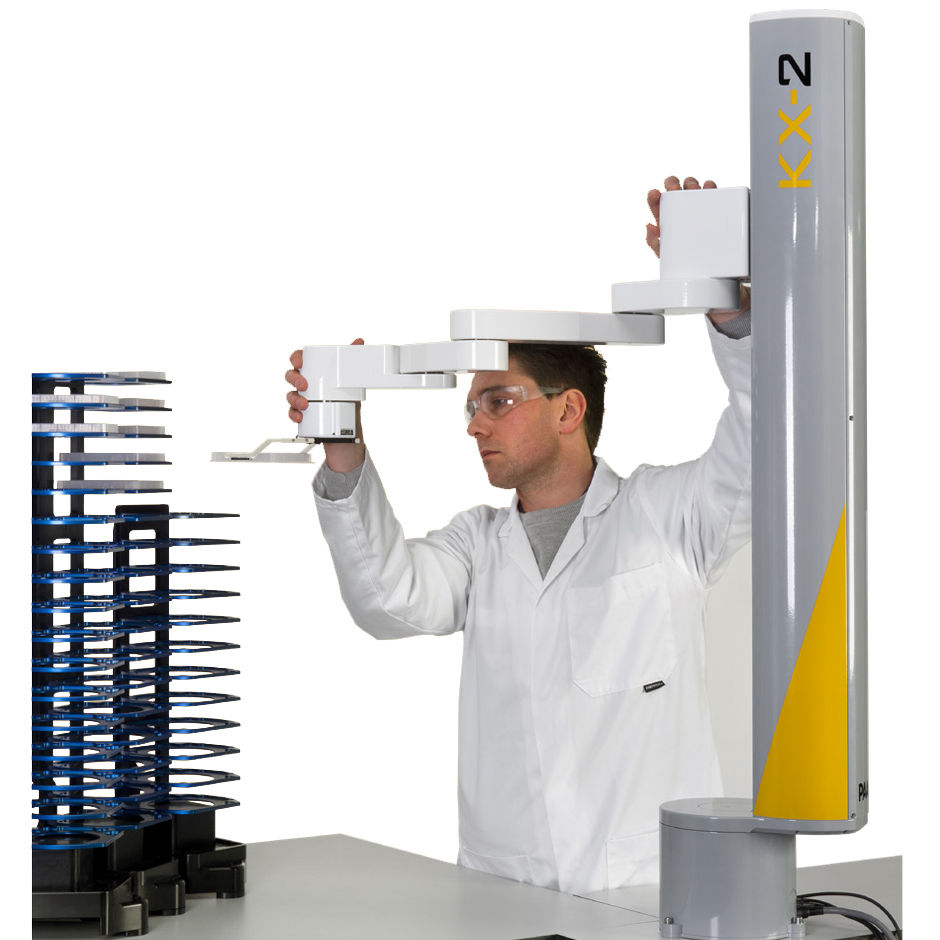
-
Flexible 360° continuous rotation of the shoulder and wrist axes and a multi-link arm, the KX-2 offers extensive reach for effective with radial compactness for best use of the available space.
-
Easy to decontaminate. The KX-2 was developed with contamination minimization in mind. The sealed design is wipe-clean with no bug traps, making it well-suited for Biosafety Level 2 applications.
-
Intelligent motion control. The linear rail and robot execute synchronized motion simultaneously. This improves efficiency and simplifies setup.
-
Easy to integrate USB interface provides easy connection to host PC. Linear rail and KX-2 can be added to existing systems, expanding capability and throughput.
-
Standard IO built in Digital and Analogue I/O available at the linear rail connector panel for interfacing and controlling other devices.
-
Simple to set up and easy to use. The KX-2 features drag-to-teach technology, providing easy automation of workflows. Simply move the robot arm to the correct position and press the button. Positon is maintained and plate gripped on power loss.
Key Benefits KX-2 Laboratory Robot

-
Flexible Available in 500, 1000, 1500 and 2000mm lengths
-
Key benefits. Larger work area. Drag-to-teach with same software as the KX-2, the rail is treated as another robot axis
-
High Speed A maximum speed of 750mm/s allows the linear rail to move quickly from one end of a large system to the other. This limited to 410mm/sec for collaborative applications.
KX-2 Linear Rails
-
Barcode reader identify labware, inventory racks or stacks
-
Plate sensor detect labware in the gripper

barcode reader

plate sensor
Key sensors as standard
KX-2+ New capabilities
Blended moves
Combining fluidity and precision for seamless transitions.
Increased payload to 1kg
Now with an increased payload capacity of 1kg.
Integrated vision with machine learning
Featuring integrated vision enhanced by machine learning capabilities.

Advanced route planner
Discover our sophisticated route planner designed to optimize travel efficiency and streamline logistics.
Mobile robot integration
Efficiently integrate mobile robots for enhanced automation and operational efficiency.
Dual handed gripper option
Explore our dual-handed gripper solution for versatile handling and enhanced automation capabilities.
KX-2 Inverted Robot
Flexible
With 360° continuous rotation and a multi-link arm, the KX2 maximizes space efficiency. Its compact arm design allows for easy instrument accessibility
Easy to decontaminate
The sealed design is wipe-clean with no bug traps, making it well-suited for Biosafety Level 2 applications.
High Safety
The KX2 is fully compliant with safety standards: ISO 10218–1:2011.


Simple to set up and easy to use
KX2 features drag-to-teach technology providing easy automation of workflows.
Flexible handling
The counter-balanced arm of the KX2 allows the handling of full deep well plates at maximum extension for optimal use of the work envelope.
Robots Specifications
KX-2
30.97in / 786.7mm (side grip)
Radial reach
7.6in / 193mm
Radial width
20.7in / 525mm
Radial stroke
KX-2 500: 19.69in / 500mm
KX-2 750: 29.53in / 750mm
KX-2 1000: 39.37in / 1000mm
Z-travel
Shoulder & Elbow: Harmonic Drive gearboxes Z & wrist: driven by timing belts Rail: helical planetary gearbox
Motors
Magnetic absolute encoders on robot joints
Encoders
500 g (1.1 lbs)
Payload
Drag-to-teach-point One touch teach button on robot
Teaching
Programmable LED array
Status light
E-stop allows use in large integrations
E-stop
Onboard I/O for direct peripheral control
I/O
Fully compliant in accordance with Category 3 Safety Standards
Compliance
KX-2 Inverted
500g (1.1lb)
Max Payload
525 mm (20.7in)
Radial Stroke
787mm (31in) w/ Side-Grip Fingers, 677mm (26.6in) to Wrist Center
Radial Reach
190mm (7.47in) with Gripper Facing Inward
Radial Compactness
Shoulder: 360° Unlimited
Z: 500mm (19.69in)
Elbow: 525mm (20.7in)
Wrist: 360° Unlimited
Gripper: 26.15mm (1.03in) per finger
Travel
Shoulder: 145 deg/s
Z: 750 mm/s (29.5 in/sec)
Elbow: 467 mm/s (18.4 in/sec) avg.
Wrist: 500 deg/s
Gripper: 47 mm/s (1.85 in/sec)
Speed (Max)
Shoulder: 14.5Nm (128 in-lb) Peak, 7.3Nm (64 in-lb) Continuous
Z: 43.3N (9.7 lbs) Peak, 21.7N (4.9 lbs) Continuous
Elbow: 11.3Nm (100 in-lb) Peak, 5.7Nm (50 in-lb) Continuous
Wrist: 1.22Nm (10.8 in-lb) Peak, 0.61Nm (5.4 in-lb) Continuous
Gripper: 22N (5 lbs)
Torque/Thrust
Shoulder: 8,388,608 counts/revolution
Z: 3,998 counts/mm
Elbow: 13,375 counts/mm avg.
Wrist: 16,384 counts/revolution
Gripper: 3,183 counts/mm (motion of single finger)
Encoder Resolution
Arm Extend: +/- 0.1mm (.004in)
Vertical: +/- 0.1mm (.004in)
Weight: 29.5 kg (65 lbs)
Height: 925mm (36.4in)
Repeatability
Input Power: 100-240 VAC), 1Φ, 47-63Hz, 5.6A Max @ 115VAC (2.8A Max @ 230VAC)
Output to Robot: 57VDC/5.3A/300W Max, 24VDC/3A/80W Max
Power Supply Dims: 240mm x 160mm x 90mm (9.5in x 6.3in x 3.5in)
Safety: Current & Position Error Sensing, Emergency Stop Button (Stop Cat. 1)
User I/O: 3 Digital Inputs, 2 Analog Inputs, 3 Digital Outputs
Power
Magnetic Absolute on robot joints, Incremental on gripper
Encoders
Drag-to-teach-point, one-touch teach button on robot, game controller (Teach Plate is included).
Teaching
Top-Grip (included), Side-Grip (included), Side-Grip-Portrait-Jog, Custom
Gripper Options
USB 2.0
PC Interface
Linear Rail
750 mm/s (410 mm/s for collaborative applications
Speed (Max)
1200 mm/s2
Acceleration (Max)
LRKX2-500: 19.69in / 500 mm
LRKX2-1000: 39.37in / 1000mm LRKX2-1500: 59.05in / 1500mm LRKX2-2000: 78.74in / 2000mm
Travel
LRKX2-500: 41.22in / 1047 mm LRKX2-1000: 60.91in / 1547mm LRKX2-1500: 80.59in / 2047mm LRKX2-2000: 100.28in / 2547mm
Overall Length
LRKX2-500: 23kg (50.7lbs)
LRKX2-1000: 31kg (68.3lbs)
LRKX2-1500: 38kg (83.8lbs)
LRKX2-2000: 47kg (103.6lbs)
Weight
Drag-to-teach-point, one touch teach button on robot
Teaching
17-bit Absolute (Absolute encoders mean the linear rail always knows where it is – right out of the box and even after power failures).
Encoders
8192 counts/mm
Encoder Resolution
Safety
The KX-2 Robots are CE marked and compliant to all current international standards.
Inherently safe - KX-2 Robot
ISO 10218-1:2011
Collaborative safety - KX-2 Robot
TS 15066
Control system safety - KX-2 Robot
BS EN 13849-1 2015
Emissions - KX-2 Robot
CSIPR11/FCC Class A
EMC - KX-2 Robot
IEC 61326-1:2012
Electrical safety - KX-2 Robot
IEC 61010-1:2010
Linear Rail
Position Error Sensing
(Stop Cat. 1) - Linear Rail
Emergency Stop Button
Have questions or need assistance?
We're here to help!
Whether you have inquiries about the KX-2 Collaborative Laboratory Robot, need technical assistance, or want to explore customization options, we're just a message away.
Fill out the form below or use the provided contact information, and one of our representatives will get back to you promptly.